The recent surge in the popularity of additive manufacturing is perfectly explainable. Design tools are readily available, and people are embracing technology in an increased capacity. That said, many users of additive manufacturing systems are still making simple design mistakes that are massively impacting their end products. Here are five top tips for better additive manufacturing designs:
1. Utilize the freedom
Subtracting manufacturing, injection molding, and other conventional design techniques don’t come with the freedom additive manufacturing offers. For instance, injection molding requires uniform wall thickness and radiused corners, among other production prerequisites. Computer numerical control (CNC) manufacturing, on the other hand, is inefficient in the production of such complex geometries as internal channels since there is no way to get the tool to the center of the part.
3D printing doesn’t come with any of these limitations. Parts are built layer by layer, giving you the freedom to create parts with labyrinths of components such as mid-build inserts, lattice structures, and internal channels. This flexibility gives you the freedom to dream up the wildest design ideas and implement them.
2. Don’t fear parallelization
3D printing systems can create a complete part in just one printing run, meaning you won’t need to go through additional assembly and finishing steps. For higher throughput, however, you may need to use more than one 3D printer simultaneously, in a process known as parallelization.
The costs of acquiring more than one printer may be high, but the advantages are ultimately bound to outweigh the cons, particularly if you are going to use the systems regularly. Parallelization has been shown to reduce material wastage by 90%, consolidate fabrication steps, minimize per-board fabrication, and eliminate retooling steps.
3. Pay special attention to the deposition time
Using 3D printers to build parts helps designers circumvent redundant design processes. However, proper 3D printing scheduling requires familiarity with deposition time. This is determined by several factors, including the number of parts produced and raw material weight. The size and weight of a 3D print can assist with deposition time estimation, although an equally accurate estimate can be reached by building test coupons.
4. Trust in data-based scheduling
When there is a single command center unifying all your 3D printing assets, deposition data can be collected during production. This enables you to measure fabrication times and use the data to tweak production scheduling.
Data-based scheduling is particularly essential in production processes where various product variants call for different printing and assembly times.
5. Digitize post-production procedures
Despite the automation of many additive manufacturing processes, most 3D printing companies still go about post-production procedures manually. Processes such as assembly and plating can take plenty of time and manpower to finish.
Automation not only saves you the hassle of real-time supervision but also reduces your overall cost of production.
Endnote
The evolution of 3D printing seems to be taking a steeper trajectory each day. The future is definitely easier and more seamless, but you don’t have to wait to up your game. Use the above tips to simplify your production processes and minimize the costs of production.
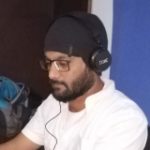
Kamran Sharief
Related posts
Sidebar
Recent Posts
The Rise of Legal Tech Startups: What Law Firms Need to Know
Introduction The legal profession, often rooted in tradition and resistant to change, faces a technological revolution. Legal tech startups are…
Shiba Inu vs. Dogecoin: The Battle of the Meme Coins
In the realm of cryptocurrency, there has been an ongoing battle between two popular meme coins, Shiba Inu and Dogecoin….
Review 5 Tips for Additive Manufacturing Designs.